The design goal of the flux for aluminum casting Given the many deficiencies of the current domestic and foreign fluxes, this topic intends to develop a new multi-functional granular refining flux with slag removal as the main and degassing as the auxiliary, which can achieve the following goals
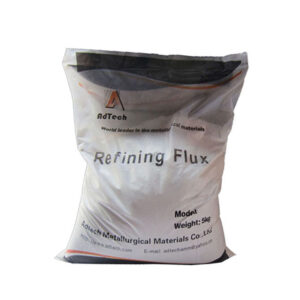
flux for aluminum casting
(1) The new the flux for aluminum casting achieves multifunctionality, that is, it integrates the triple functions of covering, slag cleaning, and slag removal to effectively cover the aluminum melt, and efficiently remove impurities (the size of the inclusions is smaller than the hydrogen content and less than 01m/l00gAl), and the powdery dry slag
(2) No obvious alkaline (earth) metal impurity elements are introduced into the melt after the new flux is refined (3) The new flux should meet the requirements of environmental protection as much as possible, and the content of harmful gases generated during the refining process
(4) Exploring a suitable new process for flux preparation to achieve homogenization of flux components (5) The cost of new fluxes is low (raw materials for flux configuration should be sourced from a wide range, stable in quality, and moderate in price).
Flux Removal Theory
31 Flux Covering Properties
Figure 2 is a schematic diagram of flux spreading on the surface of molten aluminum. Let the interfacial tension between the flux for aluminum casting and the molten aluminum be σFM: the surface tension of the flux is σF: the surface tension of the molten aluminum is σM: the wetting angle between the flux for aluminum casting and the molten aluminum is θ, then the three of σF-M, σF and σM The relational expressions are as follows (1) and (2):
(σF-X)+(σFcosθ)=σX (1)
cosθ=σx-σf-x / σf (2)
Equation (2) shows that the larger σM, the smaller σF and σF-M, the larger cosθ and the smaller θ, that is, the better the coverage performance of the flux.
32 flux separation performance
The coverage performance and separation performance of the flux are two opposite processes, as shown in Figure 3. Therefore, it can be seen from formula (2) that the smaller σM, the larger σF and σF-M, the smaller cosθ and the larger θ, that is, the better the separation performance of the flux for aluminum casting.
Flux mainly relies on its adsorption wetting or immersion wetting to achieve the purpose of slag removal. Li et al. pointed out that the type of flux-wetting inclusions is determined by the relationship between the spherical cap radius R of the molten salt and the size L of the inclusions, as shown in Figure 4. When 2R<L, the flux adheres to the wetting inclusions: When 2R>L, the flux immersed in the wetting inclusions assumes that the volume of molten salt droplets is V, flux, and inclusions.
Assuming that the volume of the molten salt droplet is V, the wetting angle between the solvent and the inclusions is θ, and the radius of the spherical cap is R, then v can be expressed as [9]
V=πR^3 / 3 (2-3cosθ+cos^3θ) / sin^3θ