Therefore, it can be inferred that both SCUT-type and B-type the aluminium casting flux have a better-degassing effect, the degassing ability is comparable, and is better than A-type refining flux. It can be seen from Figure 9 that the number of pinholes on the cross-section of the pinhole sample before refining is large. After the type flux is refined, the grade of the pinhole sample is evaluated by the national standard GB η6.3-1999. Type A flux corresponds to the 2-level pinhole sample. The B-type and sCUT-Ⅰ-type fluxes all correspond to the Ⅰ-level pinhole samples, and the ADCl2 alloys refined by the three fluxes are all qualified products.
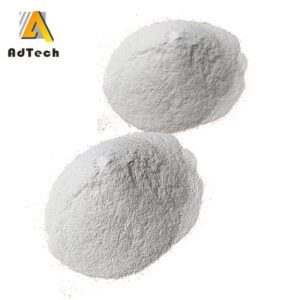
aluminium casting flux
After refining with the three fluxes, the metallographic group of the alloy has significantly reduced pores and slag inclusions, no large-sized inclusions, and a K value of 0. After the A-type the aluminium casting flux is refined, the hydrogen content is 0.139ml/Al, the hydrogen removal rate is 6805%, the gas slag content is 0.144vol%, the gas slag reduction rate is 89.22%, and the oxygen content is 8ppm (converted to oxidation Aluminum is 5 pm) After refining B type and SCUT-l type, the hydrogen content is 0.095ml/l00A1, 0.09ml/l00Al, the hydrogen removal rate is 78.16%, 79.31%, and the gas slag content is 0036vol%, 0.031vol%, respectively, the reduction rate of gas slag is 97.31%, 97.68%, and the oxygen content is 5ppm and 3ppm respectively (respectively 10ppm and 6 pm when converted into alumina). Compared with the A-type flux, the B-type and ScUT-l-type fluxes have better purification effects. In addition, it can be seen from Fig. b) that there is relatively sufficient silicon phase transformation in the alloy. By analyzing the sodium content in the alloy after treatment with different fluxes (see Table 3), it can be seen that compared with the alloy before refining, the A-type alloy has The sodium content in the alloy after flux treatment increased significantly, from 0.∞002lwt% to 0.00l66wt%, which exceeded the minimum concentration of sodium content for the fully modified silicon phase – the sodium content in the alloy after flux treatment of 0.00lwt. Compared with that before treatment, the sodium content in the alloy remained unchanged before and after treatment with SCUT-Ⅰ flux.
In addition to the purification effect, the slag-cleaning effect of the aluminium casting flux is also crucial. The three fluxes all produce powdery slag after refining. The order of aluminum slag particle size corresponding to type A, B, and SCUT-1 fluxes from large to small is B> SCUT-1> A, and the aluminum slag contains aluminum The amount of aluminum slag is 54wt%, 9.5wt%, and 8.2wt% respectively, but the amount of aluminum slag corresponding to type A flux is the largest. : On the other hand, the additional amount of A-type flux is relatively the largest. Therefore, the type of flux not only has a good slag-cleaning effect but also has relatively minimum oxidation and burning loss of molten aluminum.