The high-purity aluminum degassing unit fiber module and foamed aluminum dihydrogen phosphate fiber module are used for the rotor protection sleeve. The first design is exposed to the atmosphere of molten aluminum, and the tie rod screws and gaskets fall off due to carbonization and thermal expansion. The tie rods and nuts are pre-buried in the insulation layer. It is essential to design a rotor boot material that protects the screws and tie rods.
The R&D department of the company analyzed the material characteristics of the original rotor protective sleeve and designed a material that is lightweight, not easy to crack, and ideal for thermal shock.
1. Precautions:
1. Protect the pull rod screws of the rotor protective cover to prevent carbonization; 2. Prevent the thermal insulation layer from falling off due to the thermal expansion of the tie rod screws; 3. It is particularly important to design a material with good thermal insulation properties, easy construction, and a low drying temperature rise curve; 4. Taking into account the acid atmosphere factor in the working state of the degassing box of the online degassing unit, design an acidic rotor protective sleeve material; 5. Consider the suitability of the heat-resistant embedded parts and the fire-facing surface (30-50mm); 6. Consider the rotor protective sleeve material and The expansion coefficient between the heat-resistant steel bars needs to be improved by adding 2mm of electrical tape or painting 2mm of asphalt paint, and the horizontal tie rods of the embedded parts need to be removed;
2. Raw materials:
1. Newly developed X-140 dry powder
2. Pure calcium aluminate cement (A-80)
3. High-precision microbeads (40-80 mesh)
3. Mixing process:
Weigh the dry material of the rotor protective sleeve, 0.1% retarder; pour into the mixer and stir for 2 minutes, then run 28.5% binder (weight ratio S30: water = 1:1), and stir for 5 minutes, (Note: Observe the change of the mud material during the mixing process, and then add 1-2% binder as an adjustment), discharge, and vibrate to form.
4. Firing system: according to the company’s small-piece firing system
5. Effect:
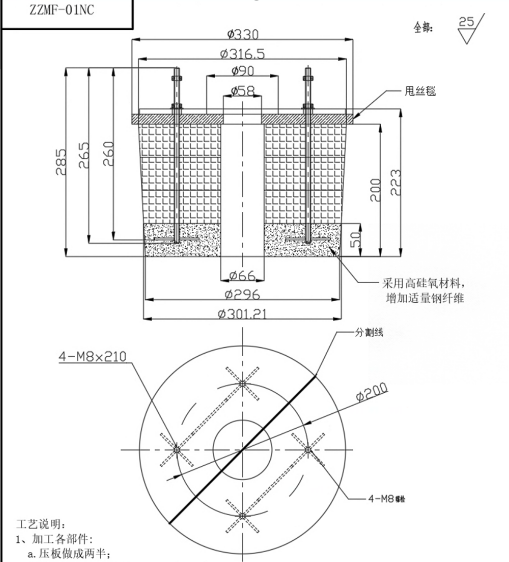
Degassing unit rotor protection sleeve design drawings
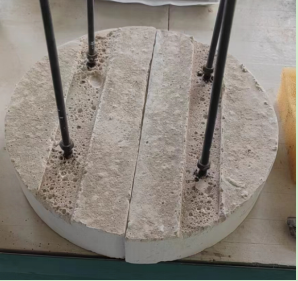
Rotor protective cover new material molding
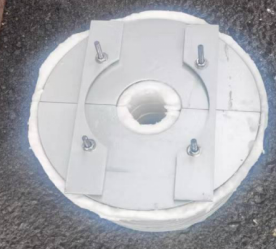
Rotor Boot Assembly
(1) Below 800°C, the thermal shock resistance is relatively good, and there is no peeling, crack, or deformation
(2) Between 800-1018°C, due to structural and other problems, the material also undergoes partial crystal transformation, resulting in deformation of the material, but there is no peeling or cracking. It shows that the material is better used at 800°C, between 800-1018°C, and the material does not show bad thermal vibration, but according to the crystal transformation, it is recommended to use it below 800°C, in special cases 800-1018 ℃ can be temporarily excessive.
Adtech main products: porous ceramic filter