the research method of ceramic filter for casting.
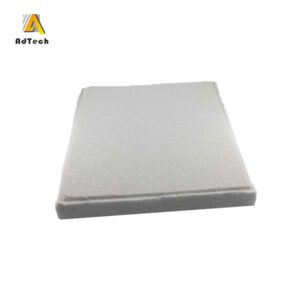
ceramic filter for casting
1.3 The significance of the topic selection and research content This work
is to develop a large-area porous ceramic filter plate with high porosity and high strength in response to the requirements of a large domestic aluminum plant for the filtration of aluminum alloy melts. This work is in the early stage of its work. part of the research work. It is expected to prepare large-area porous ceramics with uniform pore size and appropriate pore size distribution, to reduce material cost and make them industrialized. Based on the above points, the research contents of this work are summarized as follows:
Using low-cost raw materials to prepare porous ceramic filter plates with high porosity (open porosity between 80 and 90 vol%) suitable for the actual production of aluminum alloy casting.
- Reasonably adjust the relationship between the porosity and the strength of the porous ceramic filter plate.
- To study the relationship between the properties, composition, and preparation process of alumina and cordierite porous ceramics respectively.
- The research method of ceramic filter for casting
Chapter 2 Research Methods
There are various preparation methods for porous ceramics, and different methods can prepare porous ceramics with different porosity and different pore morphology. Among them, the organic foam impregnation process has attracted much attention because it can prepare foam ceramics with high porosity and three-dimensional network pore structure. At the same time, the method also has wider market value because of its simple equipment, low cost, and easy popularization. In this work, porous ceramic filter plates were prepared by the organic foam impregnation method.
21 Preparation process
Process flow
After the organic foam precursor is pretreated, the foam is first extruded to remove the air, and then immersed in the ceramic slurry, so that the foam naturally stretches in the slurry, and absorbs the slurry, so that the slurry can fully infiltrate the organic precursor. ; Then squeeze the slurry for a short time and knead it repeatedly to make the slurry evenly adsorbed on the mesh wire of the precursor network structure, and finally dry and burn. The process flow of this experiment is shown in Figures 2-1. Organic foam paste
2.1.2 Selection and pretreatment of organic foam precursors
The organic foam materials suitable for the preparation of mesh porous ceramics are generally polymer sponges made by a specific foaming process, and the materials are often polyurethane (polyurethane), polyvinyl chloride, polystyrene, latex, cellulose, etc. Polyurethane foam is selected in this test, because of its low softening temperature, it can avoid the damage of thermal stress in the process of volatilization, prevent the collapse of the green body, and ensure the strength of the product.
Because the pore size of open-cell organic foam determines the pore size of porous ceramics (usually 2~25 pores/cm), 30ppi, 26ppi, and 23pi polyurethanes were selected in this work according to the product’s requirements for pore size and porosity. sponge foam
Since the raw material foam precursor has many inter-network films, excess slurry left on the inter-network film during dipping will cause the product to block pores. Therefore, in this work, pretreatment is adopted to remove the inter-network film, that is, the organic foam precursor is immersed in a 15w% NaOH solution, hydrolyzed at a temperature of 40-60 °C for 4 hours, and then repeatedly rubbed and rinsed with water, and dried for use.