Aluminum Alloy Melting and Refining Metal Melt
(1) Solid liquid ratio: according to the charging amount required by the product specification, the solid material with solid-liquid ratio of 40% and electrolytic aluminum liquid of 60% is specified.
(2) Charging sequence: when the furnace temperature reaches above 800 ℃, the charging shall be started. First, the bulk material shall be reinforced, and then the electrolytic aluminum liquid shall be added.
(3) Smelting requirements: after the electrolytic aluminum liquid is added, start the electromagnetic stirrer for stirring for 20 min, and then start the electromagnetic stirrer to stir for 20 min after the molten aluminum is completely melted, so as to ensure the alloy melt composition and temperature uniformity; when the aluminum liquid temperature rises to above 730 ℃, manual mixing shall be carried out, and the original sample shall be removed for analysis, and the composition shall be adjusted according to the analysis results.
(4) Pre refining of melt in smelting furnace: since 60% of electrolytic aluminum liquid is used for batching, and the electrolytic aluminum liquid has the characteristics of high temperature, high impurity content and high hydrogen content, in order to ensure the melt refining and on-line treatment effect in the holding furnace, carbon tetrachloride is used to pre refine the melt in the smelting furnace, so as to reduce the slag content, hydrogen content and alkali metal content in the melt It’s sodium.
(5) Sampling analysis and converter: after the completion of pre refining, the furnace temperature of holding furnace must be 800 ℃ when the composition is suitable and the temperature reaches 740 ℃.
(6) Refining of aluminum melt in holding furnace: the mixed powder of high-purity argon loaded hexachloroethane and sodium free refining agent is used for powder spraying refining of aluminum alloy melt, and the refining time is not less than 20 min.
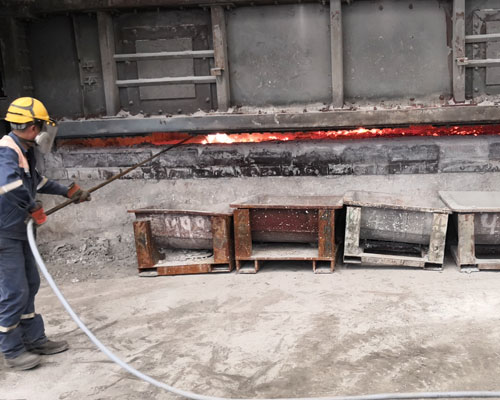
Refining Metal Melt