In the field of automobiles and airplanes, there are more and more applications of large aluminum alloy parts, and the requirements for parts are getting higher and higher. In addition to ensuring the chemical composition, mechanical properties, and dimensional accuracy, the castings are not allowed to appear shrinkage, porosity, leakage, slag inclusion, and other defects. The Purification Treatment of Molten Aluminum is one of the basic methods to produce high-quality aluminum castings, and it is also the main method to improve the comprehensive performance of aluminum alloy.
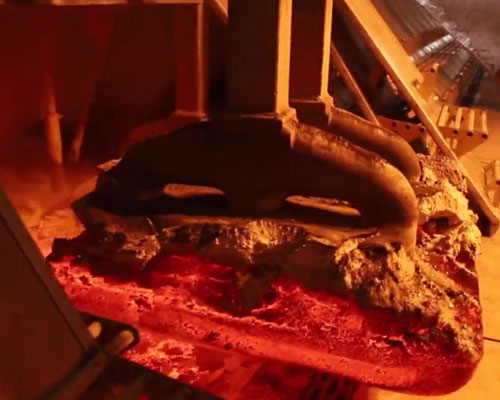
Purification Treatment of Molten Aluminum
Purification Treatment of Molten Aluminum
The refinement effect of aluminum alloy melt has an important impact on porosity, porosity and the formation of inclusions, and directly affects the physical properties, mechanical properties and service properties of aluminum castings. If there is no high-quality molten aluminum alloy, even if the subsequent modification and grain refinement treatments are effective, once defects are generated in the casting, they will still stubbornly exist and are difficult to compensate, and it is difficult to imagine high-quality castings.
Therefore, foundries attach great importance to the gas and inclusions in the cast aluminum alloy melt, and take various purification measures to eliminate the gas and inclusions. Aluminum foundries generally use bubble floatation degassing and CFF filtration methods to remove gases and other non-metallic impurities in molten aluminum.
Bubble Floatation Degassing
The bubble floating method is to pass inert gas (such as nitrogen, argon, etc.) into the aluminum melt to form bubbles. Hydrogen in the melt diffuses into these bubbles under the action of partial pressure difference, and is eliminated with the rising of bubbles, so as to achieve the purpose of degassing. In the process of floating, bubbles can also absorb some oxidized inclusions to remove impurities.
The effect of the bubble floatation method depends on the nature and purity of the inert gas on the one hand, and also on the size and dispersion of the bubbles in the melt. If the bubble diameter is smaller, the bubble is more uniform and dispersed. The specific surface area of the bubble is larger, the distance of hydrogen diffusion into the bubble is shorter, the bubble floats slowly, and the degassing rate is higher. The rotary blowing method is the best method in the blowing method. It mainly depends on the shape and speed of the rotating head, and controls the size and distribution of the bubbles by breaking the bubbles. The rotating head is the technical core of these methods.
CFF Filtration Method
CFF filtration method is the most economical and the most convenient filtration method. When the aluminum fluid flows through the ceramic filter holes, inclusions are adsorbed on the inner surface of the ceramic plate and the gap cavity due to the combined effect of axial pressure, friction, and surface adsorption. Generally speaking, the thicker the ceramic plate, the smaller the hole, the slower the flow rate of liquid aluminum through the ceramic plate, and the better the filtering effect.