The basic principle of an induction Induction melting furnace is a type of air-core transformer, the induction coil is equivalent to the primary winding of the transformer, and the metal within the crucible Induction melting furnace charge is equivalent to the secondary winding of the transformer (load). When in the primary winding through the intermediate frequency current (500-2500 weeks/second or higher) the role of the electromagnetic field under the influence, produce magnetic line secondary windings, Cause the charge induction potential, and vertical to the axis of the induction ring in the surface-induced current (eddy current), so that the material itself heats the metal charge melting.
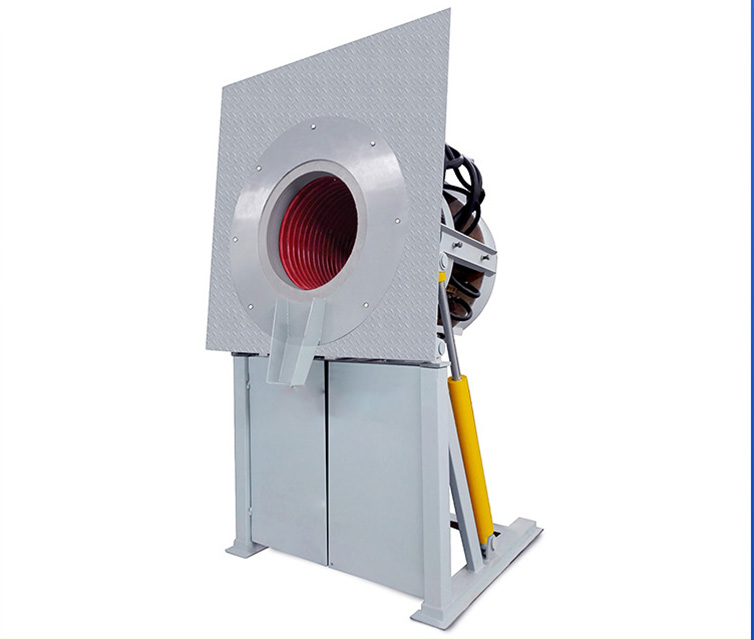
Induction melting furnace
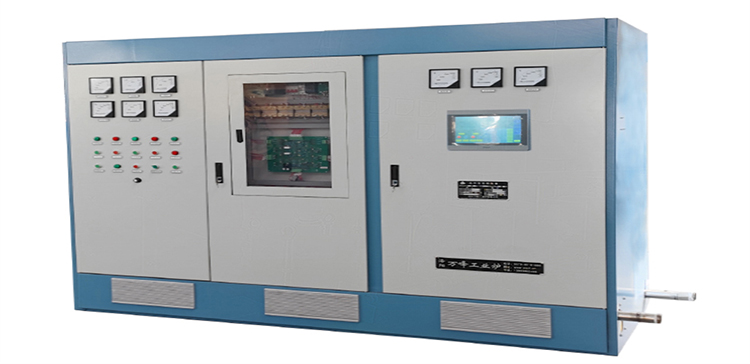
Induction melting furnace
The power supply is a frequency conversion device that uses a trace or IGBT to convert a 50-week three-phase power frequency current into a medium and high-frequency current with a frequency of 300HZ-3600HZ. Its working principle is through a three-phase bridge rectifier circuit, the 50 weeks / s of power frequency AC rectified into DC, after a filter, and finally, the warp-inverter will turn DC into a certain frequency of AC supply load, so this inverter is actually an AC-DC-AC converter. Constant power energy-saving medium Induction melting furnace, after a long period of the production practice test, has been generally praised by users. It has been improved on the original basis to make its performance more excellent, the current naturally crosses zero, easy to turn off, so the operating frequency is higher.
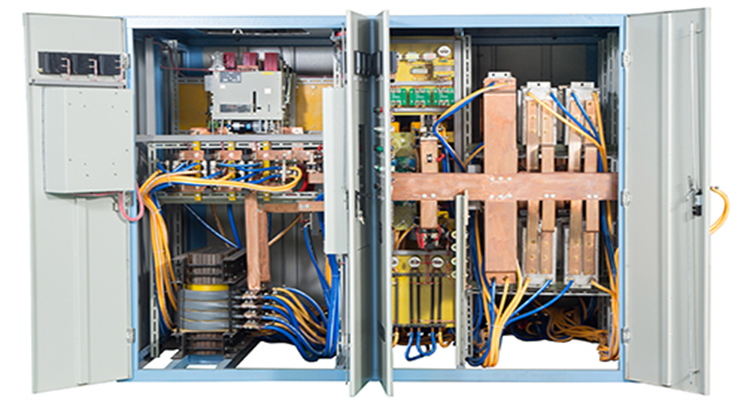
Induction melting furnace
Saving Medium Induction melting furnace Advantage:
1. High melting rate. During melting, the power is kept running in the optimal frequency band, minimizing the undesirable effects of the new furnace scale on the melting rate
2. The power factor is high, and the power factor can reach more than 97% during the operation of the whole machine
3. No interference to the power grid
4. Energy saving of more than 10% of electricity consumption
5. The startup success rate is high, and the startup success rate under any debt is 100%
6. The main control board adopts a connector interface, which is more convenient to maintain
7. The inverter adopts a series thyristor to reduce the damage rate of the thyristor
The reasons why the medium frequency melting aluminum furnace is widely used in the aluminum industry:
1. The intermediate Induction melting furnace has less aluminum melting loss than the power frequency furnace;
2. The medium-frequency aluminum melting furnace is more efficient than the resistance furnace;
3. The medium-frequency aluminum melting furnace can increase the melting rate by increasing the power;
4. Under the same power, the intermediate frequency aluminum melting furnace is less noisy than the power frequency furnace, and the smoke and dust pollution is less.