The filtering result of the honeycomb ceramic filter depends on the chemical composition of the inclusions in the melt, the shape of the ceramic foam filter plate, the filter plate specifications, the metal flow rate, the wettability of the filter plate surface to aluminum, the size of the inclusions, etc.
Honeycomb Ceramic Filter for Molten Aluminum
Many studies have shown that when a melt containing inclusions passes through the ceramic foam filter, the inclusions are trapped on the surface of the particles. Inclusions larger than 30um are filtered by mechanical interception, and inclusions smaller than 30um are retained by surface tension. When the melt containing inclusions passes through the porous ceramic filter, the filtration efficiency is related to the following factors:
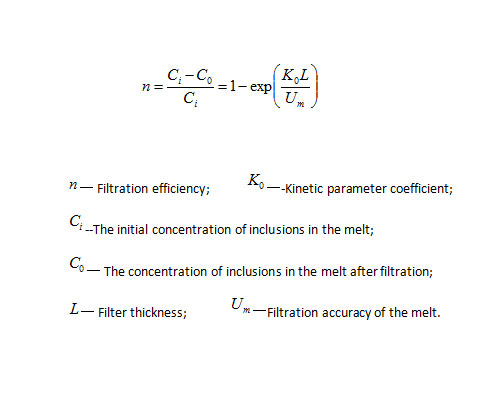
Filtration Efficiency
The kinetic parameter K, and the ratio of the honeycomb ceramic filter thickness L to the melt flow rate determine the filtration effect. Increasing the thickness of the filter, reducing the pore size, reducing the flow rate, and increasing the chance of impurity collision, the greater the probability of inclusions being retained, deposited, and adsorbed on the pore wall, the better the filtering effect.
When the flow rate is low, the inclusion particles are more likely to deviate from the flow line and are adsorbed by the filter. When the flow rate is too high, the aluminum liquid flow will wash away the solid inclusions from the hole and take it away. So multi-stage filtration systems with different thicknesses and meshes can achieve good filtration results.
Porous Ceramic Plate Instructions
The CFF filter box should be thoroughly cleaned before use, so as to prevent the residue of refractory material falling into the aluminum liquid.
The size and specifications of the porous ceramic plate and the filter box should be matched, and the matching gap and deviation angle between the two should be as small as possible.
When the filter is used, the head is large before the aluminum melt passes through. After the melt passes through the alumina ceramic foam filter, the head is rapidly reduced, generally about 5mm. But with the use of the filter, the pores are gradually blocked by slag, which hinders the passage of the melt. And the liquid level difference on both sides gradually increases until the flow through the filter cannot meet the requirements of casting, now, it needs to replace a new filter.