As the carrier of the filter, the performance of the reticulated polyurethane foam plastic directly affects the Foam Ceramic Filter Manufacturing Process. It should have the following characteristics:
- The mesh is uniform to ensure the free penetration of the ceramic slurry and the coating is uniform.
- The hydrophilic property can firmly Absorb the slurry.
- Sufficient resilience, can quickly restore the original shape after extruding the excess slurry.
- Medium temperature volatility, volatility below the ceramic firing temperature, and does not pollute the ceramic.
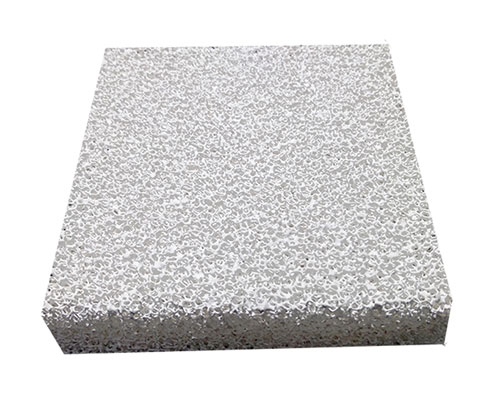
Foam Ceramic Filter Manufacturing Process
The ceramic foam slurry is made of refractory aggregates, sintering aids, binders, and other micropowders with water. The preparation of the slurry is a crucial process for Foam Ceramic Filter Manufacturing Process. The ceramic slurry should have the highest possible solid content (the slurry Density 1.8~22g/cm3, solid content 50%~65%), good thixotropy and wettability. The high solid content ensures that the ceramic particles are attached to the foamed plastic screen to the maximum extent, and the strength of the filter is improved. The good thixotropy facilitates the uniform shaping of the slurry and prevents plugging. If the wettability of the slurry and the ceramic foam is poor, the slurry will gather at the intersection of the foam structure, and there are fewer ridges, the strength will decrease after sintering, and even waste products.
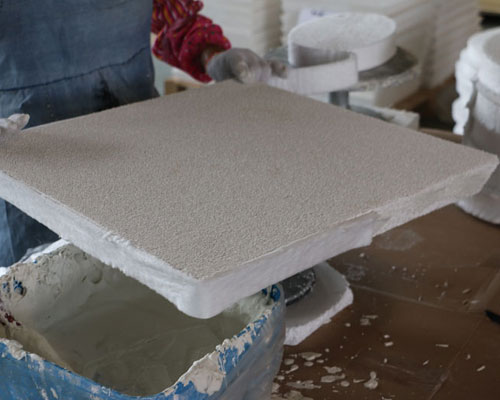
Foam Ceramic Filter Manufacturing Process
Additives and refractory aggregates can form a low melting point phase or undergo solid-phase sintering. If the additive amount is not appropriate, it will hinder low-temperature sintering.
- Fluoride has a very obvious effect on reducing the sintering temperature of ceramics, but fluoride will corrode equipment and pollute the environment.
- ZrO2 significantly improves the fracture toughness of the corundum ceramic foam filter. Magnesium oxide and titanium oxide enhance its sintering density.
- SiO2+AO3 can lower the sintering temperature of the silicon carbide filter.
- Rare earth oxides and refractory clays can shorten the sintering time and lower the sintering temperature of bauxite ceramic filters.
The binder can be divided into room temperature and high-temperature binder, its function is to improve the strength of the blank. Normal temperature filters generally use organic binders, which volatilize with foam after medium temperature; high-temperature binders generally use inorganic binders. But sometimes the binder will reduce the high temperature performance of the filter, so some slurry does not add the binder.
Saturate and immerse the ceramic slurry with foam plastic, and then repeatedly squeeze the foam plastic to remove the excess slurry, so that the ceramic particles are fully and uniformly attached to the foam plastic to make a green body. The key to this process is the strength and uniformity of the extrusion. If the ceramic slurry remains in the foam, it will cause defects such as smaller pore size or plugging. On the contrary, too little ceramic slurry adhesion will affect the strength of the product.