The fixed degassing unit is installed in a fixed position and works in the manner of a moving ladle. High-speed rotating graphite introduces a quantitative amount of refined gas into the melt. Through the relatively high shearing force of the graphite rotor and the molten aluminum, small bubbles are generated and evenly distributed in the aluminum melt. Since the hydrogen partial pressure in the bubble is zero, the hydrogen partial pressure in the aluminum melt is relatively high, and the hydrogen in the liquid aluminum gradually diffuses into the bubble. At the same time, the metallic and non-metallic inclusions in the liquid aluminum are adsorbed on the surface of the bubbles, and the bubbles and inclusions float, thereby removing the hydrogen and inclusions in the liquid aluminum.
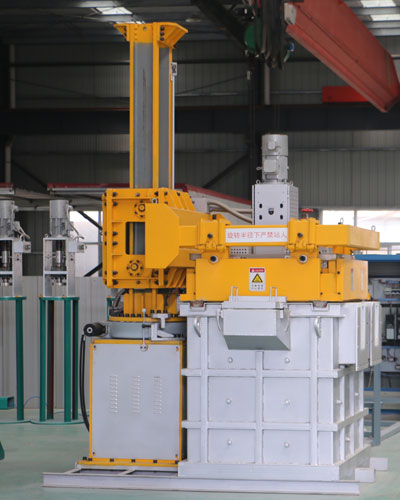
Fixed Degassing Unit
Fixed Degassing Unit Degassing Process
The liquid aluminum is stirred by a controlled rotating graphite and a rotor, while a metered inert gas is pressed into the liquid aluminum through a flow divider, the bubbles are evenly dispersed in the solution metal, and the air pressure of the bubbles is zero. Due to the high partial pressure of hydrogen in liquid aluminum, hydrogen in liquid aluminum continuously diffuses into bubbles. At the same time, some non-metallic inclusions in liquid aluminum are adsorbed on the surface of the bubbles. Useless hydrogen and inert bubbles attached by some non-metallic inclusions will float to the surface of the liquid. It can improve the purity of liquid aluminum in a short period of time, reduce the scrap rate, increase production efficiency, improve the mechanical properties of castings, and enhance the competitiveness of products, which cannot be achieved by traditional degassing methods.
After degassing, a large amount of convection is formed in the degassing box, so that small bubbles can fully diffuse into the liquid aluminum. At the same time, the fixed degassing unit adopts a sealed design to prevent secondary pollution caused by outside air entering. Greatly improve the degassing efficiency of the equipment.
After each casting, the residual aluminum liquid in the degassing box can be discharged, which greatly promotes the rapid conversion of the alloy and eliminates the furnace cleaning of the degassing device during the alloy conversion process. It can reduce metal loss and improve production efficiency.
The design of the degassing device is simple and easy to use, which is especially suitable for occasions with small workshop space, and can reduce the workload of infrastructure in the process of equipment transformation. At the same time, the different requirements of users for the quality of castings are considered in the equipment design. The degassing device can be upgraded to allow the molten aluminum to pass directly without on-line refining, thereby reducing the production cost of the enterprise.
In the design of the degassing device, the convenience of equipment maintenance is fully considered. Taking into account the convenience of equipment maintenance and graphite rotor replacement, the rotating nozzle part can be rotated 180 degrees, so normal production can still be carried out even when the equipment is maintained.