Grout spraying amount of ceramic foam filter
The amount of slurry spraying is an important index to measure whether the spraying effect is ideal
It is also an important factor to determine whether the spraying of each green body is uniform. So many
The company will index it and set specific parameters for different specifications of filter plates. To ensure
Verify that the product spray meets the process requirements and reaches the specified spray effect.
For filter plates of different specifications and sizes, the amount of slurry spray is different.
Of course, for the slurry with different water content, the spray volume is also different. Table 1
The spray volume of several common specifications of filter plates in our company is listed.
It can be seen from Table 1 that the spray weight and the surface area of the green product exist
A certain relationship. Namely: m=s × (0.04~0.06)
Where, m is the weight of single-side shotcrete (g);
S – single surface area of green body (cm2).
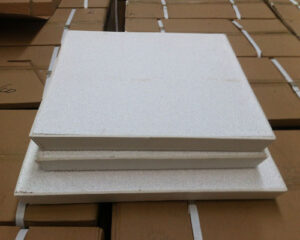
ceramic foam filter
Conclusions about the ceramic foam filter process
The particle size, water content and shotcreting volume of the shotcreting slurry all affect the shotcreting effect
Plays an important role. Among them, the size of the slurry determines the dispersion, uniformity and final surface sintering of the spray; the water content of the slurry affects the consistency of the slurry; the consistency of the slurry
It determines the effect of roughening the mesh on the surface of the green body: the amount of spray is the measure of the amount of spray
Whether it meets the important parameters of process requirements.
Alumina foam ceramic filter plate has a good demand for shotcreting process
Disadvantages. The advantage is that the surface of the filter plate has been greatly improved, especially the surface contacting with the bearing plate when it is dry. Its surface is rough and the mesh wire will be fine. spray
After slurry, the surface of the fired filter plate is smooth, and the mesh line is correspondingly thickened. Wet spray
The disadvantage of slurry is that it can only be sprayed on one side; The disadvantage of dry billet spray is that the spray will turn the green body and cause certain damage to the green body. Especially for the thin and large green body, the product will even appear cracks after sintering. So for thin thickness and large size
The slurry spraying process is not recommended for the filter slab body of, but wet spraying can be selected
Pulp. In addition, guniting increases the production cost and delays the production cycle. pen
It is believed that for filter plates of common specifications, the shotcreting process is still needed,
To meet the market’s demand for the appearance and internal quality of products.