Typical structure of ceramic filter unit used in some factories. The shell of this kind of ceramic filter is welded with 10 mm thick, lined with aluminum silicate fiber felt, and then laid with a layer of light refractory brick and coated with talcum powder inside. A and B chambers are separated by porous ceramic plate or silicon carbide plate. Room A is the filter chamber, the filter pipe is assembled on the diaphragm hole, and the assembly part is sealed with aluminum silicate fiber felt. Room B is the storage room, collecting the filtered metal. The upper part of the filter is provided with a heating cover and a resistance heating wire inside. Thermocouple continuous temperature measurement, electronic potentiometer automatic control filter metal temperature. The melt enters into the filter chamber a connected with the flow-through from the furnace, then seeps out through the micropores of the filter tube, collects in the storage chamber, and finally enters the crystallizer through the flow tray.
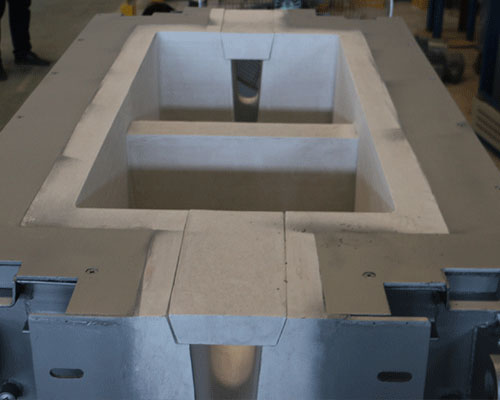
Ceramic Filter Unit
The main technical parameters of the ceramic filter unit are: filtration precision, filtration efficiency, filtration rate, initial head.
Filtration precision is also called purification precision. It can be expressed by the maximum size of the solid inclusion passing through the porous ceramic, or the minimum size of the solid impurity retained by the filter medium. The filtration accuracy of ceramic filter mainly depends on the pore size and filtration process of porous ceramics. The smaller the pore size is, the slower the filtration speed is, and the higher the filtration accuracy is. The higher the filtration accuracy, the greater the tendency of feather crystal formation.
Filtration efficiency: refers to the percentage of solid impurities removed and the concentration of solid impurities in the melt before passing. The filtration efficiency mainly depends on the pore characteristics of the filter media (maximum pore size, pore size distribution, etc.), the particle size distribution of solid impurities in the melt and the filtration conditions. Generally, the filtration efficiency of ceramic filter increases with the decrease of filtration speed and the extension of filtration time.
Filtration rate. It refers to the volume of melt passing through the filter medium per unit area in unit time. It is the main basis for designing filter productivity. The filtration rate mainly depends on the permeability coefficient, thickness and the liquid level difference between the two sides of the filter medium. The larger the permeability coefficient and pressure difference, the smaller the medium thickness, the faster the filtration rate. The permeability coefficient increases with the increase of porosity and pore size and the decrease of melt viscosity.
Blocking rate: refers to the amount of solid inclusions retained in the unit volume of filter media per unit time. The size of this value indicates the service life of the filter. Because it is very difficult to measure the blocking rate, the pressure drop after passing through the filter increases with the blocking when the filtration speed is constant. Therefore, the increase of pressure drop is often used to represent the blocking rate of the filter. The blocking rate is directly proportional to the melt throughput and the inclusion content in the melt, but inversely proportional to the total volume of the filter media and the through porosity.
Initial head: refers to the pressure head required for the melt to flow through the channel of the filter medium. Because aluminum melt is not wettable to corundum matrix material, the interfacial tension between them is very large. When the melt enters into the micropores of the medium, a convex meniscus will be formed, and the surface tension will prevent the melt from advancing. The smaller the medium channel and the lower the temperature, the larger the initial head.