In the modern aluminum melt purification process, Casting Filters filtration is the last purification process close to the casting terminal. Before that, 6 ~ 80% of inclusions and gases have been removed through flux refining in furnace, medium and non-media adsorption, but finer inclusions (generally < 15m in particle size) are distributed in the melt (including secondary inclusions produced by chute and tundish). In order to obtain high-performance aluminum products, these fine inclusions must be gathered and separated by adsorption. Compared with other purification methods, filtration method has become the preferred process for terminal purification of aluminum melt due to its low energy consumption, convenient operation, high impurity removal efficiency and less secondary pollution.
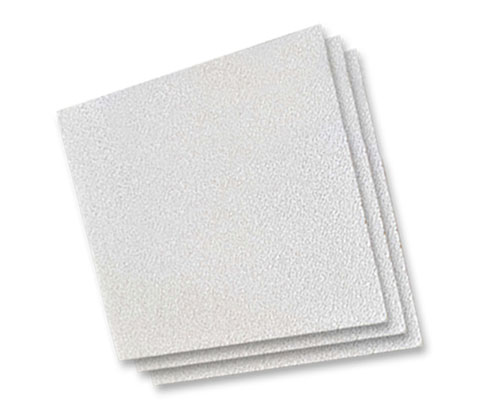
Casting Filters
Common Aluminum Melt Casting Filters
Glass fiber cloth and mesh filter mainly rely on mechanical interception to separate inclusions. They are simple in structure and low in cost. They are suitable for filtering large particle inclusions. However, the filtering effect on fine inclusions is very small. In addition, the filter screen has low thermal strength, short service life and unstable filtration, so it can only be used once. Therefore, it is mainly used for primary filtration of melt
DBF has the advantages of high efficiency, large filtration capacity, long service life and good regeneration. However, there are some problems such as high replacement cost, short circuit and inclusion desorption caused by disturbance, and small particle size of filter ball will lead to capillary resistance. Therefore, DBF is suitable for melt filtration with high performance requirements and large treatment capacity
Ceramic particles combined with plate or tubular filter (BPF) are sintered with alumina or silicon carbide particles of 2 ~ 5mm diameter and special binder. The filtration is mainly carried out by zigzag gap between particles. Its advantages are high thermal strength, low surface energy, low initial pressure head, high filtration efficiency (especially for inclusions less than 20m), large filtration capacity, low synthetic cost and so on, High price, suitable for mass production of high-end aluminum products. The product can be rinsed and used for more than 20 days, but the product is mainly used at present
Honeycomb (straight hole) filter is similar to automobile exhaust gas filter. It is extruded by die or sintered after molding directly. It has the advantages of high strength, low filtration resistance, stable melt flow rate, convenient replacement and low cost. However, due to the limitation of molding die, the hole diameter is large, and the filtration mainly depends on the wall of the hole to absorb impurities, and the filtration efficiency is low.
Ceramic foam filter (CFF) is currently the most widely used filter for aluminum melt filtration. Its advantages are high porosity, high filtration efficiency, easy replacement, low cost, and strong adaptability. Ceramic Foam Filter can filter solid inclusions and separate part of liquid Inclusions. The disadvantage is that the high temperature strength is low, the life is short, and the amount of filtration is small.