Ceramic fiber filters filtration technology is one of the filtration technologies developed rapidly in recent years. Compared with the traditional granular filter material, the fiber filter material has larger specific surface area, larger interface adsorption, and can intercept suspended solids, so the filtration effect is good. Compared with foam ceramics, it has smaller pore size and higher filtration accuracy. Compared with organic fiber filter, ceramic fiber has good thermal stability, chemical stability, and thermal shock resistance. Ceramic fiber has been widely used in air purification, high temperature flue gas filtration, chemical filtration, diesel exhaust particulate capture, liquid metal filtration, and so on.
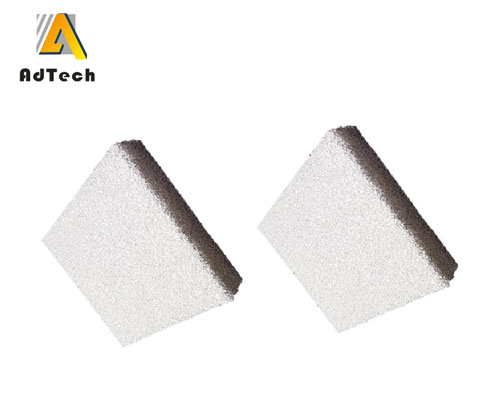
Ceramic Fiber Filters
Ceramic Fiber Filters Classification
Ceramic fiber paper is made by imitating the papermaking process of ceramic fiber, binder and additives through automatic and continuous chemical processes such as pulping, forming, curing and drying. The product has white color, flexible texture, good flatness and excellent machining performance. Ceramic fiber filter paper is a kind of high efficiency filter material. The filter material has the advantages of low flow resistance, high filtration efficiency, low thermal conductivity, high temperature resistance, corrosion resistance, non-toxic and stable chemical properties. It has been widely used in large-scale integrated circuits, instruments, pharmaceutical preparations, bioengineering, air purification in ultra clean studio and so on.
Ceramic fiber mesh (cloth) is a kind of ceramic fiber textile, which is made of spun cotton yarn and reinforced yarn. Ceramic fiber textiles have low thermal conductivity, chemical corrosion resistance and high temperature resistance, which are mainly used for metal liquid filtration. So as to reduce the slag content, improve the cutting performance, improve the surface quality and product qualification rate.
Ceramic fiber filter is a kind of porous material, which uses the textile characteristics or fine shape of fibers to form three-dimensional holes. The forming methods include fiber braiding, winding and vacuum filtration forming.